Saving tomorrow today: Pursuing sustainability measures is a growing priority for agenciesSaving tomorrow today: Pursuing sustainability measures is a growing priority for agencies
Saving tomorrow today: Pursuing sustainability measures is a growing priority for agencies
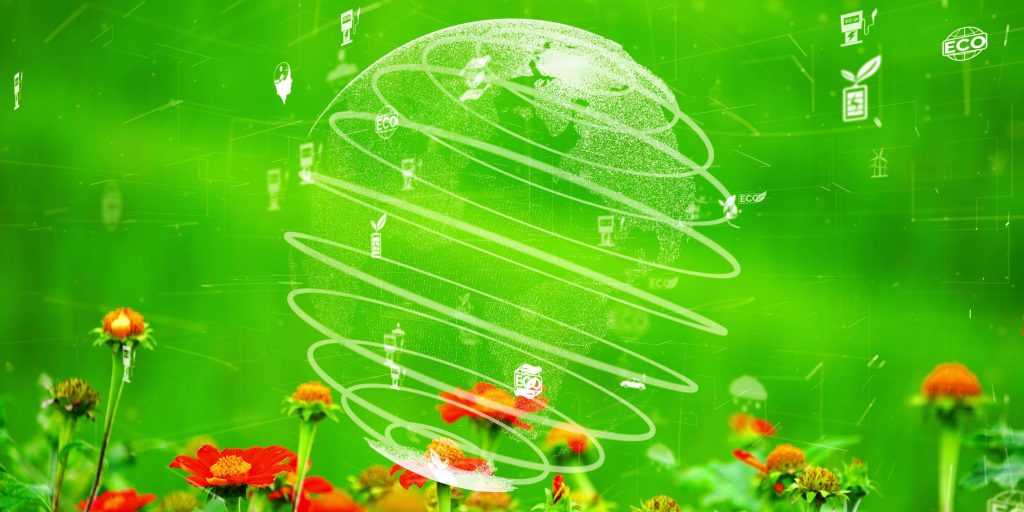
Written by Tammy Rimes
Pursuing sustainability measures is no longer the latest new fashion. Instead, it’s becoming a necessity to minimize waste sent to landfills, preserve natural resources, lower greenhouse emissions and protect the health of local communities. Government agencies collectively, through both small and large initiatives, can reap huge environmental benefits.
California takes the lead in carpet landfill diversion
More than 250 million pounds of carpet is discarded in California landfills every year. Realizing the need to divert this waste from landfills, the state passed AB2398, creating the California Carpet Stewardship Program (CARE). Carpet America Recovery Effort—based in Dalton, Ga., the carpet capital of the world—was selected as the stewardship organization for California.
Since its inception, more than one billion pounds of carpet has been collected through more than 100 public and 200 private drop off sites in the state.
This hard-to-recycle product, made largely from fossil fuels, can present challenges for collection and recycling. Old carpet is torn out, sorted by fiber type and transported to a recycling facility. Specialized equipment removes the backing from the fiber and the separated materials are then further processed into fiber and pellets. The post-consumer carpet results in fibers or plastic pellets used to make a broad range of products, including new carpet, carpet tiles, carpet underlayment, and products for the automotive, transportation and construction industries. Marketing efforts include a specialized catalog to help consumers identify and select products due to their recycled content.
Executive Director Bob Peoples, with a PhD in chemistry, has been active with recycling efforts since 2002, and is excited about the current state of the program. During the first quarter of 2022, CARE hit a record 18.1 million pounds of recycled output. Peoples notes, “We grow by at least 20 percent in recycling rate annually, and already off to a good start this year. It took a few years to get the program infrastructure in place, and since 2015 progress has been excellent.”
Planting trees and saving paper
Saving paper starts at the source—trees. Georgia-Pacific is the world’s leading paper provider in the United States and has committed to a 1:1 philosophy. The approach is simple—at least one tree is planted for each tree used. As a result, the number of trees has increased in U.S. forested areas, making forest growth exceed harvest every year since the 1950s. While many regions of the world face forest loss, the United States is one of the few countries increasing forest area based on the 2020 United Nations Food and Agriculture Organization report.
“One hundred percent of the wood used in our facilities is grown within surrounding regions and supports local tree farmers. Those farmers go to great lengths to responsibly grow, harvest and replant the trees as part of the local landscape and economy,” says David Brabham, Georgia-Pacific’s director of stewardship strategy. “We are proud to be part of that forest stewardship story.”
Municipalities traditionally rely on paper-intensive processes, especially in procurement offices where paper bids are issued for hard copy responses from suppliers. PlanetBids President and Co-founder Arpie Zavian states, “When the pandemic hit, many teams were forced to address this issue head-on. Incoming requests rose significantly when government employees were sent home, and suddenly, everyone was interested in automation.”
An agency that took the initiative to overcome this obstacle was the Inland Empire Utilities Agency located in Southern California. Contracts Administrator Robert Wallin says, “Picture going through 500 pounds of paper binders just to determine initial compliance.” And that was just one bid process. Through automation, the agency achieved their goal of instituting a fully paperless procurement process.
Zavian says, “Moving to automation saves more than just trees. It saves car emissions from eliminated drive time to a government office, while cloud computing reduces on-site storage requirements so that file cabinets filled with documents will no longer be required.”
Experts provide guidance
Whether it’s city council chambers, employee offices or front counter reception areas, a large spend category for any government entity is furniture. However, measuring sustainability in furniture manufacturing and purchasing can be complicated. Proactive organizations rely on third party experts who administer rating systems, set high standards and offer partnership opportunities.
EcoVadis, the world’s largest provider of business sustainability ratings, scores companies on environment, labor and human rights, ethics, and sustainable procurement. Its sought-after gold level includes commitments to cut greenhouse gas emissions as approved through an independent Science-Based Targets initiative. As one of those gold-rated companies, Steelcase has also been recognized by the Environmental Protection Agency (EPA) for its commitment to scrap reduction in manufacturing, with a 25 percent reduction in fiscal year 2022.
According to Mary Ellen Mika, director of sustainability for Steelcase, “We believe in protecting our environment. Some of our forward-thinking government customers have included challenging sustainability requirements in their purchasing contracts that go way beyond the norm. It’s a positive sign that customers care deeply about sustainability and aren’t satisfied with unsubstantiated marketing claims.”
The Government Services Administration, for example, routinely requires BIFMA level certifications. BIFMA is a not-for-profit trade association for business and institutional furniture manufacturers promoting sustainability in commercial furniture with measurable standards. The Public Works and Government Services of Canada agency requires any chairs sold into their organization meet some of the most stringent BIFMA-level standards.
When furniture has reached the end of its useful life, there is growing interest in its proper disposal. “Take back” programs have been created by several national furniture manufacturers, where old office furniture is donated to non-profits or recycled to avoid unnecessary landfill waste. For example, Kimball International collaborates with non-profit Green Standards to provide a sustainable solution for redistribution of furniture. Operating in more than 100 countries, this organization has achieved results of only 1 percent of waste going to landfills, rather than 80 percent in a standard office liquidation.
According to Lacey Fischer, Kimball’s public sector marketing manager, “This holistic approach blends two ways of thinking: office furniture is manufactured and sourced as well as ultimately disposed of in environmentally conscious ways, capturing the entire lifecycle of the product.”
Saving water going down the drain
Many municipalities are responsible for local sewer lines running underground throughout their communities. General maintenance and clearing pipe blockages are typically carried out by a combination (jet/vac) truck. Each truck carries hundreds of gallons of fresh water, includes a high-pressure water pump, and features a vacuum system to draw debris and dirty water back into the truck.
While these trucks are effective in keeping sewers flowing, a shortcoming is the amount of clean potable water used during the process. At 80 gallons per minute pressure, a typical truck can be emptied in 19 minutes. The operator must then drive to a fire hydrant or water source to continually refill the tank. The result? Massive amounts of fresh water become contaminated and must ultimately be processed at the sewage treatment plant.
With water becoming a diminishing resource, new recycling combination trucks are gaining a foothold in municipal operations. The contaminated water that is vacuumed into the tank is processed and re-used for jetting operations. The truck can then operate all day with one tank of water, saving thousands of gallons per day of operation. While the initial fill-up may be potable water, it could also operate with water from the sewer pipe or a treatment plant basin. Under the right conditions, the use of potable fresh water can be eliminated altogether.
A compounding problem for traditional recycling trucks is the large amount of cooking grease and sediment that often clog truck filters. According to Tom Hochmuth, municipal regional sales manager for Sewer Equipment, “We have started to forgo the use of filters in favor of a five-stage passive separation process. For example, the Genesis Water Recycler from Cappellotto by Sewer Equipment relies on the natural tendency of greases and oils to float while sediment sinks. By skimming, spinning and dumping the grease and debris out of the dirty water, this new technology achieves high-water purity after the final stages.”
Water conservation is just the tip of the iceberg. Not having to continually drive to a fresh water source or dump dirty water throughout the day results in fuel savings and increased crew productivity. Hochmuth continues, “The effectiveness of using a passive separation process allows the cleaning of pipes, while prolonging the life of the pump, plumbing and jetting nozzles.”
Transitioning fleet operations
With wildly fluctuating gas prices and increased focus on lowering emissions, municipalities have been transitioning fleet operations toward environmentally friendly options. Auto makers are responding in a big way by offering more than 770 electric vehicle (EV) models worldwide by 2030—more than three times the number currently available. The electrification of medium- and heavy-duty commercial fleet machinery such as mowers, emergency vehicles, transit buses, garbage trucks and construction equipment is also gaining traction.
One example is the world’s first all-electric compact track loader the Bobcat T7X, recently announced by Bobcat. Powered by lithium-ion batteries, the loader produces no emissions. Using a fully electric drive system in place of a traditional hydraulic system, it is comprised of half the parts and components required for a diesel-engine loader, driving down maintenance and overall ownership costs.
As the technology is new, Brent Coffey, director of product line management with Sunbelt Rentals Inc., states that a special partnership was created between the two companies. “Over the past two years, we tested this equipment on active job sites to demonstrate its ability to complete whatever job is needed. Whether the task is hauling trash, moving snow, digging holes, or moving pallets full of materials, we wanted to ensure an electric option could do it all.” The tests proved a new EV equivalent can conduct the work currently done by traditional equipment.
One surprising result of these site tests has been a safer and more productive worker experience. Brent continues, “We found in a typical work site, the electric equipment is so much quieter. Although this might require workers to be more observant due to the quiet nature of the equipment, it also creates a better work environment for the machine operator.”
According to Bill Collins, government sales director for Element Fleet Management, several factors should be considered for a comprehensive sustainable fleet program. Crucial components include specialized driver training on the nuances of operating an EV, comprehensive driving plans to minimize trips and assist emergency or 24/7 vehicles, and an infrastructure for proper charging stations within the jurisdiction.
With government mandates calling for zero carbon emissions by 2030-2045, electrification is top of mind for many public sector fleets. Collins states, “We are seeing more governments become proactive in the EV arena, with incoming requests asking for guidance. By taking incremental measures or a ‘pilot first’ approach, many entities are achieving successful larger-scale efforts in reducing their overall carbon emissions while optimizing the fuel economy of their existing internal combustion engine fleets.”
Capturing sunlight to clean air
In Ohio, the city of New Albany operates a robust public services department housed in a large garage featuring an angled roof. The roof provided a unique opportunity for city leaders to implement part of their vision: to utilize alternative energy sources by outfitting a city property with solar panels.
To install 5,570 square feet of solar panels, New Albany accessed Gordian’s Job Order Contracting (JOC) solution through Sourcewell. JOC is an Indefinite Delivery/Indefinite Quantity (IDIQ) construction project delivery method that can reduce costs and shorten timeframes. After evaluating the project, Gordian brought in McDaniels Construction and subcontractor Third Sun Solar to install the panels. Using JOC enabled the project to be completed in just eight weeks. The newly installed solar panels remove 112 metric tons of carbon dioxide from the air every year.
In addition to a positive social impact, the project also achieved budgetary savings. The new solar panels will cut the complex’s electricity bill in half.
Small steps count, too
Living in New York City, Tracy Rosensteel became alarmingly aware of the problem of plastic pollution while walking her French Bulldog Indiana Jones through the streets of Manhattan. “At the end of each day, street corner bins were full of plastic bags full of dog waste. Using three plastic bags a day picking up after my little guy, I thought, ‘someone should do something about this issue.’”
The curious entrepreneur understood that the overuse of plastics has become a major environmental problem. Five-hundred million single-use plastic doggie bags containing 10 million tons of waste are deposited in landfills annually. In addition, plastic bags can take 500 to 1,000 years to break down or become microplastics that continue to pollute the environment. After more research, Rosensteel took up the fight against plastic pollution and launched a recycled, non-chlorine bleached paper alternative to single-use plastic dog waste bags called Pooch Paper.
Rosensteel was determined the product should be made in the United States. She states, “I found a tremendous paper plant that is carbon neutral and uses renewable energy. The sourced paper and pulp are already recycled and the pulp drying process creates a greaseless coating that is PFAS chemical free. I can’t get a whole lot greener than that.”
Working with municipalities throughout the country, these consumer-friendly dog waste stations can now be found in dog parks and neighborhoods. She concludes, “Everyone can do their part. Small steps add up to big changes to better the health of our planet.”
Tammy Rimes, MPA, is the executive director of the National Cooperative Procurement Partners (NCPP). She formally served as purchasing agent for the City of San Diego, the ninth largest city in the nation, and emergency logistics chief during the 2007 Witch Creek Fires. Under her leadership, the city consolidated its warehouse operations, centralized all purchasing and contracting operations, and moved to a more customer focused approach.