February 13, 2023
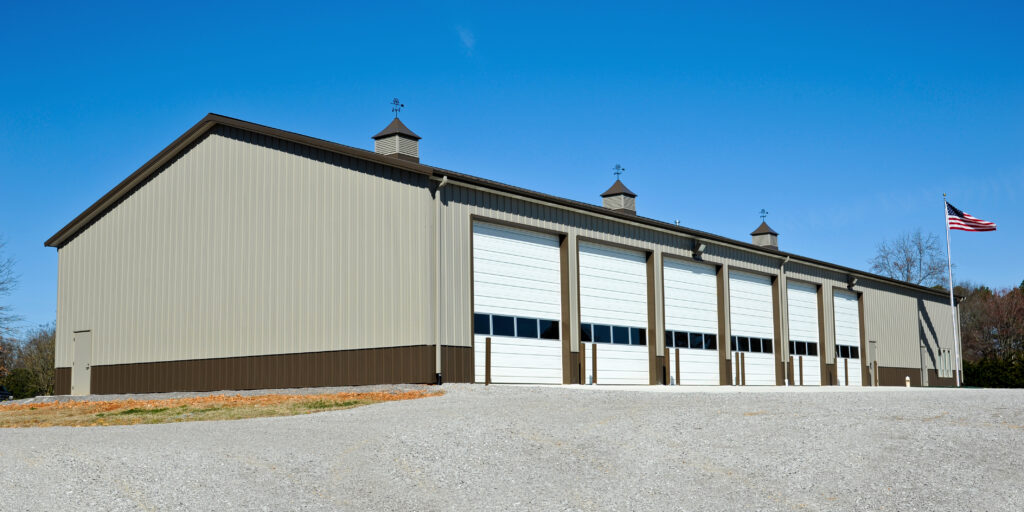
Metal buildings serve a variety of functions and purposes in government, says Tony Bouquot, general manager at the Metal Building Manufacturers Association (MBMA). “Whether it’s a government office campus, a state or county park management facility, a regional recycling complex, a city convention center or a community recreation center, many government agencies depend on metal building solutions.” He points to the following selling points—the speed of delivery; the cost-efficient materials used to build metal structures; and the long lifecycles of metal buildings that equate to tangible and quantifiable long-term value.
The MBMA official says fire stations are a great example where a metal structure works well. “More and more, you see beautiful fire facilities, clad in façade materials that complement the style and scale of the surrounding community. And when you go inside, you find secure firefighting functional areas as well as spacious and abundant areas for firefighters to live, work and play.”
Bouquot says not only are the fire stations practical and pleasant facilities, but they can also be kind to the environment. “They can embody sustainable attributes and provide opportunities for energy and environmental options, such as solar panels and roof gardens.”
Indeed, metal buildings are composed of steel and are 100 percent recyclable. Nearly every metal building component incorporates recycled steel. “An independent study reveals that, for the types of projects where metal buildings are most economical, they typically perform better in lifecycle analyses and have the least material impact on the environment,” Bouquot tells Co-op Solutions.
Metal buildings can provide governments with a versatile, clear span structure. “This means there are no required interior columns to impede the reconfiguration of spaces to accommodate changes in building use and/or expansion,” he explains.
And these kinds of structures can go up fast to meet a city’s urgent infrastructure needs. “Metal buildings are typically constructed in about a third of the time required for other forms of construction. And since all building parts are generally delivered together, there is no lag time in waiting for missing items or backordered supplies,” Bouquot explains.
He adds that metal construction ensures easy expansion. “With metal building systems, expansion typically involves the simple removal of an end or side wall, erection of additional structural frames, and matching the existing wall and roof coverings to the addition. This flexibility naturally cuts costs and reduces the time and inconvenience typically required to expand or add to an existing structure.”
Design flexibility is another characteristic of metal structures, according to Bouquot. “When a city/county wants to promote a consistent brand, they will want to use textures, colors and design elements that represent that overall aesthetic. Metal buildings provide versatility to meet each of the branding objectives.” He explains that cladding products, alternative coatings, specialized steel elements and unique structural formations can all be part of a metal building design to reach desired branding goals.
Resilience is a demonstrated characteristic of metal structures. “Through our extensive research at MBMA, we have confirmed that metal buildings are wind-, hail- and fire-resistant and can withstand hurricane and earthquake events, making them a very practical and resilient community solution. Also, the low-combustion materials comprising a metal building system can often result in insurance cost reductions over other forms of construction. This can add up to big savings for local government entities,” Bouquot states.
Metal roofing, one element of a metal building, is also quite sturdy. Roofs on metal structures have has been shown to withstand winds of 140 mph. Bouquot adds: “In seismic zones, low-weight flexible frame options offer higher resistance to tectonic forces.”
Metal buildings are engineered to provide a precise fit for each unique city/county use. Bouquot points out: “The building components are manufactured, and then all materials are delivered to the construction site as a complete package—assuring single-source responsibility and prompt product delivery.” And the construction process goes fast with metal facilities: “The standardization inherent in systems-based buildings makes design, manufacturing, delivery and building erection possible in as little as two-thirds the normal time for conventional structures.” What’s more, building erection time and costs are predictable since all parts are manufactured and shipped to the site. Shipments of materials usually take place within six to eight weeks from the time an order is submitted.
The MBMA executive suggests the following first step as government officials consider metal building construction: “Invite a metal building manufacturer and a metal building contractor to sit down and explain the logic of a metal building solution. Systems engineering is very straight-forward, and a clear description of the building design, construction, cost, and lifecycle attributes will help government officials make informed building decisions.” Go to the following link for information on MBMA members.
Bouquot offers this advice to city or county administrators who see a need for a metal building in their government operations: “Ask your building manufacturer to provide you with a fact sheet about metal buildings for you to use in community presentations and on your website. This sheet could include facts about building optimization, resiliency, environmental attributes, cost effectiveness and lifecycle expectations.” He explains that this educational data will help officials’ constituents see why the metal building option is a smart, sustainable choice.
OMNIA Partners offers a robust portfolio of cooperative contracts in the public procurement space. The firm lists several cooperative contracts under the keyword “Metal buildings.”
Michael Keating is senior editor for American City & County. Contact him at [email protected].